Digital transformation: The technology underpinning servitization
In this series of articles that are serialised from an exclusive new Field Service News two part white paper co-authored by Kris Oldland and Justin Konopaske, we will explore multiple aspects of the complex discussion of servitization…
In previous articles in this series we have so far explored the concepts discussed in the first paper in the two-part series including:
- definition of servitization for 2023,
- servitization as a spectrum,
- orchestration of the developing organizational structure
- how to navigate the transformational change needed for servitization
Now as we continue our exploration of the servitization landscape, our focus shifts to the transformative power of technology. As we have seen across each article in this series, the alignment of digital transformation and servitization is essential.
While servitization has existed for many decades, it is in today’s golden age of digital transformation that it is truly accessible.
In this article, we shall explore technological innovations that serve as guiding lights, illuminating how to overcome challenges and achieve successful servitized solutions. While the technology required for servitization may vary from case studies, some core fundamental technologies are often essential.
Intelligent Inventory Management: Empowering Operational Efficiency
In operational efficiency, the mastery of inventory management through technological intervention emerges as a cornerstone for organizational success.
Leveraging Advanced Solutions:
Advanced inventory optimization software takes the reins, reshaping the landscape of spare parts inventory management. Its sophisticated algorithms and real-time insights enable strategic decision-making, reducing excess inventory and minimizing shortages.
Real-time demand forecasting, supported by technology, offers a glimpse into the future demand landscape. The ability to anticipate fluctuations equips organizations with the agility to adjust inventory levels dynamically, avoiding overstocking or stock-outs.
Mitigating Carrying Costs:
By embracing automated replenishment mechanisms, technology introduces a seamless inventory flow, striking a balance between maintaining optimal stock levels and mitigating the financial burden of carrying excess inventory. This translates to reduced storage costs and increased working capital efficiency.
The integration of inventory management technology across the organization fosters data-driven decision-making. This synchronization enables cross-functional teams to harmonize their efforts, ensuring inventory levels align with production, customer demands, and service obligations.
The technological underpinning in inventory management is an enabler and necessary in the journey toward servitization. It equips organizations to optimize resources, enhance operational resilience, and position themselves as agile and responsive partners in the service ecosystem.
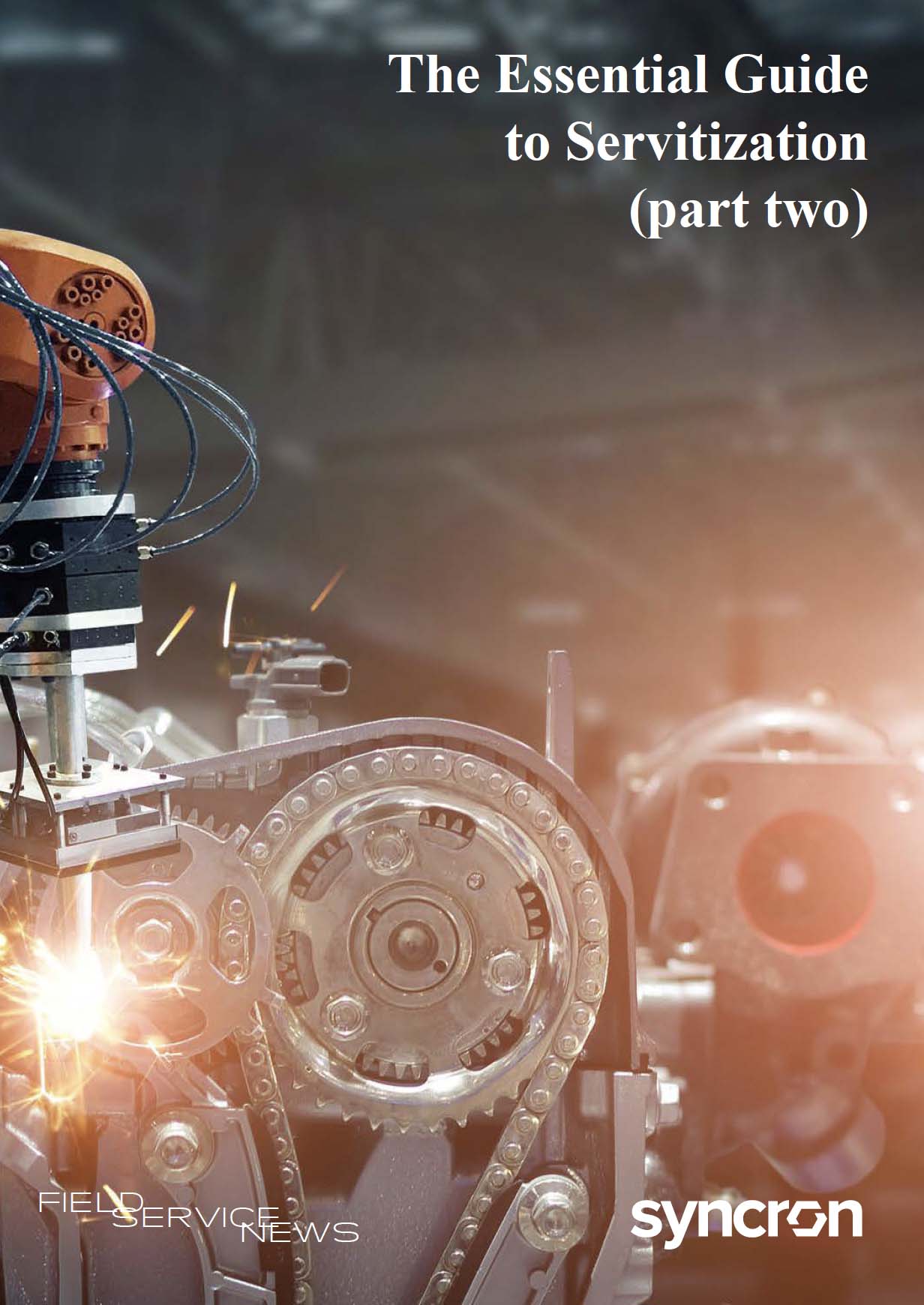
Data usage note: By accessing this content you consent to the contact details submitted when you registered as a subscriber to fieldservicenews.com to be shared with the listed sponsor of this premium content Syncron who may contact you for legitimate business reasons to discuss the content of this briefing report.
This content is available for FSN PRO members and also for a limited period for FSN FREE members. Please make sure you are logged in to access this content.
Not yet subscribed? Instantly unlock this content and more on our forever-free subscription tier FSN FREE
"The Internet of Things (IoT) forms the backbone of predictive maintenance by enabling seamless data collection from sensors embedded within equipment. These IoT-enabled sensors continuously monitor performance metrics, transmitting data to centralized platforms for analysis..."
Dynamic Pricing Dynamics: The Unveiling of Adaptive Service Pricing
Within the arena of pricing strategy, a new chapter unfolds—dynamic service pricing, a phenomenon that ushers in a paradigm shift toward adaptability and value optimization.
The Currency of Intelligence:
Dynamic service pricing tools take centre stage, orchestrating a symphony of flexibility. These tools allow organizations to tailor pricing models to the ever-changing market landscape, responding in real-time to demand fluctuations and competitive pressures.
Dynamic pricing becomes the conduit through which market intelligence is distilled into actionable strategies. Integrating variables such as market demand, customer location, and competitive benchmarks empowers organizations to balance profitability and attractiveness.
Real-Time Value Mapping:
The essence of dynamic service pricing lies in its capacity to map value in real-time. This approach ensures that customers perceive the true value of the services they receive, fostering satisfaction and loyalty.
Dynamic service pricing is more than a strategic shift—it’s a testament to an organization’s adaptability and responsiveness. It empowers organizations to navigate a complex pricing landscape with precision, forging customer relationships founded on transparency and value.
Anticipating Future Challenges: The Strategic Role of Predictive Maintenance
Within service optimization, predictive maintenance emerges as a strategic cornerstone, harnessing the power of data-driven foresight to revolutionize the service landscape.
Data-driven insight:
Data-driven predictive maintenance technology assumes the role of a seer, leveraging data patterns to anticipate and prevent equipment failures before they manifest. This capability transforms reactive maintenance into a proactive and strategic endeavour.
The Internet of Things (IoT) forms the backbone of predictive maintenance by enabling seamless data collection from sensors embedded within equipment. These IoT-enabled sensors continuously monitor performance metrics, transmitting data to centralized platforms for analysis.
However, the sheer volume of data we now have makes finding insight within it impossible without technology, and without insight, ultimately, data has no actual value. Therefore, advanced machine learning algorithms play a pivotal role in predictive maintenance. These algorithms learn from historical data to identify trends, recognize patterns, and establish correlations between factors and potential failure events. Continuous learning makes these algorithms more accurate in predicting failures over time.
Continuous learning makes these algorithms more accurate in predicting failures over time.
"Mobile tools offer the functionality to identify required parts through QR codes or image recognition, streamlining the process of ordering replacements..."
Predictive Analytics Platforms:
Robust predictive analytics platforms integrate data from multiple sources, enabling comprehensive analysis of equipment health. These platforms provide customizable dashboards, visualization tools, and predictive models that empower maintenance teams with actionable insights for strategic decision-making.
Additionally, remote condition monitoring systems provide real-time insights into the health and performance of equipment. These systems leverage data from sensors and other sources to assess the current state of machinery, detecting any deviations from regular operation and flagging potential issues for further investigation.
Mobile and Remote Empowerment:
Mobile and remote service capabilities emerge as steadfast allies when navigating the complex landscape of modern service demands. These tools enable technicians to transcend traditional boundaries and operate seamlessly across locations, improving service responsiveness and agility and providing the flexibility required for the level of service efficiency that servitization demands.
Real-Time Information Access:
Mobile solutions arm technicians with instant access to vital information, from equipment manuals to historical maintenance records. This real-time access is essential for driving first-time fix rates (FTF), critical for the service efficiency required for servitization.
Taking this further, we must explore the power of remote service capabilities. Remote service capabilities empower technicians to diagnose and troubleshoot equipment issues from a distance. Through augmented reality (AR) or even video conferencing, experts can guide on-site technicians through complex procedures, ensure accurate and efficient issue resolution, and boost critical FTF rates.
Seamless communication between field technicians, experts, and central support teams is facilitated through mobile applications. Instant messaging, voice calls, and video conferencing enable rapid information exchange, collaborative problem-solving, and real-time decision-making.
Empowering engineer efficiency:
As discussed earlier in this chapter, parts, and inventory management is crucial and mobile functionality here is also vital. Mobile tools offer the functionality to identify required parts through QR codes or image recognition, streamlining the process of ordering replacements. This reduces downtime by expediting parts procurement and replacement. This can be streamlined even further when blended with data analytics and remote monitoring.
Additionally, mobile apps allow technicians to capture performance data and readings directly from the field, ensuring accurate and up-to-date data collection. This data feeds into analytics platforms, enabling continuous improvement initiatives and data-driven insights.
Technicians can also log maintenance activities, repairs, and observations directly into mobile apps, contributing to the asset’s history. This record becomes valuable for future diagnostics, maintenance planning, and life-cycle management.
"AI’s adept analysis integrates past interactions, purchase history, and preferences, fostering deeper customer connections..."
All of these aspects allow the engineer to operate at optimum efficiency and reiterate this critical operational service efficiency. Integrating mobile and remote service capabilities significantly reduces travel time, eliminates unnecessary site visits, and enhances overall service efficiency. Technicians can complete more tasks in less time, leading to increased service throughput that will pave the way towards servitization.
AI’s Transformative Impact: The Power of Intelligence Unleashed
Within the realm of technology’s marvels, Artificial Intelligence (AI) and Machine Learning (ML) rise to prominence as central figures in a narrative marked by task automation, insight refinement, and add turbo boosters to all other digital transformation projects that will be required for servitization.
Automation Efficiency:
AI and ML stand as architects of efficient automation processes. Previously manual and repetitive tasks are now streamlined through AI-powered automation, resulting in operational optimization.
This shift relieves human resources from mundane duties and enhances overall efficiency. Forecasting, once reliant on manual analysis, is now expedited through data-driven pattern recognition, leading to more accurate and timely predictions. This orchestration of automation enhances resource utilization and operational excellence.
Personalized Experiences:
In this age of AI advancement, customer experiences are elevated through historical data analysis and AI’s analytical capabilities. AI mines intricate patterns to craft tailored customer engagements. Customer journeys evolve from generic interactions to personalized narratives aligned with individual preferences, behaviours, and goals.
AI’s adept analysis integrates past interactions, purchase history, and preferences, fostering deeper customer connections. This strategic personalization goes beyond transactions, cultivating enduring customer loyalty and advocacy.
Amid the technology landscape, a toolbox of solutions empowers organizations to navigate servitization’s complexity. Guided by AI and ML capabilities, these tools illuminate the path to outcome-oriented service excellence, aiding organizations in overcoming challenges and embracing the vast potential of the servitization landscape.
Do you want to know more?
If you want to read more from this paper then you can access it instantly on the button below if you have a sufficient membership. If you don’t have the right membership privileges then you can register on the button below for instant access.
This content is available for FSN PRO members and also for a limited period for FSN FREE members. Please make sure you are logged in to access this content.
Not yet subscribed? Instantly unlock this content and more on our forever-free subscription tier FSN FREE
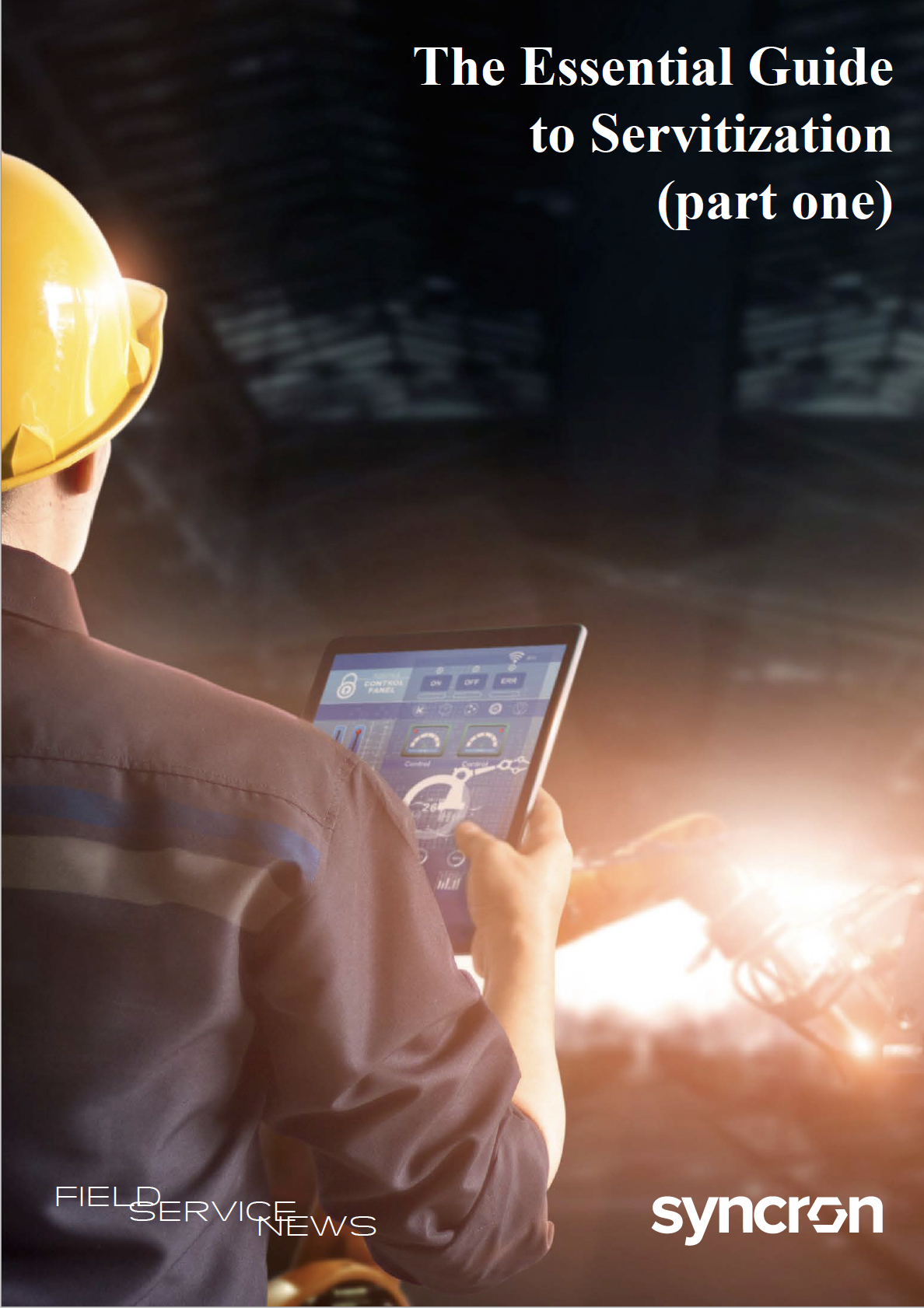
Data usage note: By accessing this content you consent to the contact details submitted when you registered as a subscriber to fieldservicenews.com to be shared with the listed sponsor of this premium content Syncron who may contact you for legitimate business reasons to discuss the content of this briefing report.
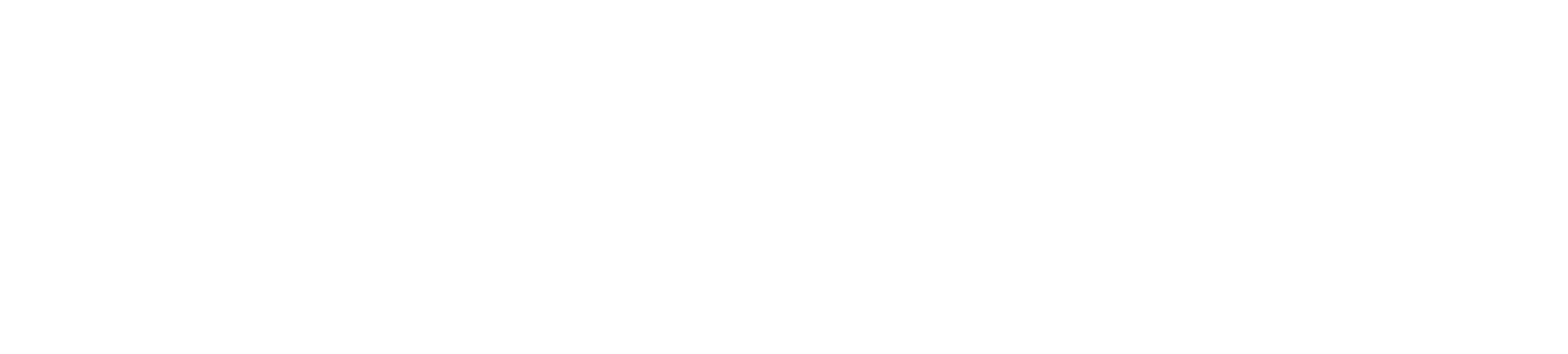