Digital Twins in Spare Parts: Smarter Stock, Fewer Surprises (But Not a Silver Bullet)
Digital twins promise smarter spare parts management, but they’re no magic fix. Companies that invest in quality data and seamless integration reap the rewards—others? Not so much…
Spare parts management has always been a high-stakes guessing game. Stock too much, and finance starts asking why your warehouse looks like a hoarder’s garage. Stock too little, and suddenly a critical machine is down, customers are furious, and you’re paying obscene amounts for rush shipping. And let’s be honest—traditional forecasting has always been part math, part gut feeling, and a whole lot of hoping for the best.
Now, digital twins are rewriting the playbook. Instead of reacting to shortages or sitting on piles of unused inventory, companies are using real-time data to predict what they’ll need, when, and where. The result? Fewer stockouts, less waste, and—most importantly—fewer “Where the hell is that part?!” moments.
But let’s not get carried away. Digital twins can be a game-changer, but they’re not a magic wand. In fact, some companies have learned the hard way that simply throwing tech at the problem doesn’t always fix it.
The Spare Parts Struggle: A No-Win Scenario—Until It Was
Johann Diaz has been in this battle long enough to know that spare parts planning used to feel like an unsolvable puzzle.
“I can’t tell you how many times I had the same argument—stock too much, and finance is livid. Stock too little, and now we’re scrambling to explain to customers why their equipment is sitting idle,” Diaz says. “It felt like we were always one step behind.”
Take the case of a major industrial manufacturer—we’ll call them Company X. When they first adopted digital twins, they thought they had it all figured out. They built detailed virtual replicas of their equipment, loaded them up with IoT data, and sat back, expecting instant efficiency.
Didn’t quite go that way.
At first, their predictions were completely off. Some parts they thought would last another six months failed in two. Others sat untouched in warehouses, collecting dust. The problem? Their data was incomplete, and their maintenance teams weren’t fully trained on how to use the system.
"Test it, prove the value, then go bigger..." Johann Diaz, Service Revolution Academy
It took months—and more than a few emergency shipments—before they got things under control. But when they did? They saw massive reductions in downtime and a leaner, more cost-effective inventory. The lesson? Digital twins work, but only if you put in the effort to make them work.
If Digital Twins Are So Great, Why Isn’t Everyone Using Them?
Now, some leaders still aren’t convinced. And honestly? I get it.
New tech always comes with risk. The last thing any business wants is to invest in a complex system that overpromises and underdelivers. Plenty of executives have been burned before—sold on software that was supposed to “revolutionize” their operations, only to find themselves drowning in IT headaches.
Diaz understands the hesitation. “The biggest obstacles?” he says. “Legacy systems, upfront costs, and—let’s be honest—people being stuck in their ways. Change is hard, even when the status quo is clearly broken.”
And he’s right. Plenty of companies hesitate because they assume digital twins require a massive, top-to-bottom transformation. But businesses like GE Digital are proving that’s not the case. Their approach? Start small, integrate with what you’ve got, and scale as you go.
“Test it, prove the value, then go bigger,” Diaz advises. “But waiting too long? That’s the real risk—because your competitors sure as hell aren’t waiting.”
Beyond Inventory: A Supply Chain That Talks to Itself
Inventory optimization is just the beginning. The real power of digital twins comes when they break down silos across the supply chain.
Take Airbus. They’re using digital twins to link suppliers, logistics teams, and maintenance crews. Everyone sees the same data, in real time, which means fewer delays and fewer last-minute scrambles.
“It’s not just about stocking the right parts—it’s about getting the entire operation in sync,” Diaz says. “The companies that figure this out? They’re going to dominate.”
"Digital twins are only as smart as the data feeding them.."
Bad Data In, Bad Decisions Out
Here’s a reality check: digital twins are only as smart as the data feeding them. Garbage inputs? You’ll get garbage predictions. And suddenly, your shiny new system is making the same dumb mistakes—just with fancier software.
That’s why IBM and others are layering AI into digital twin models, constantly refining and validating data to keep predictions sharp. The goal? No more surprises. No more stockouts. No more wasted inventory.
The Future: No More Guesswork, No More Excuses
Here’s the thing—digital twins aren’t some futuristic concept. They’re happening right now. And the companies figuring it out today? They’re the ones setting the standard for tomorrow.
So, what’s the move? Keep trusting outdated forecasts and hoping for the best? Or start playing the game with actual foresight?
Because let’s be real—hope has never been a great inventory strategy.
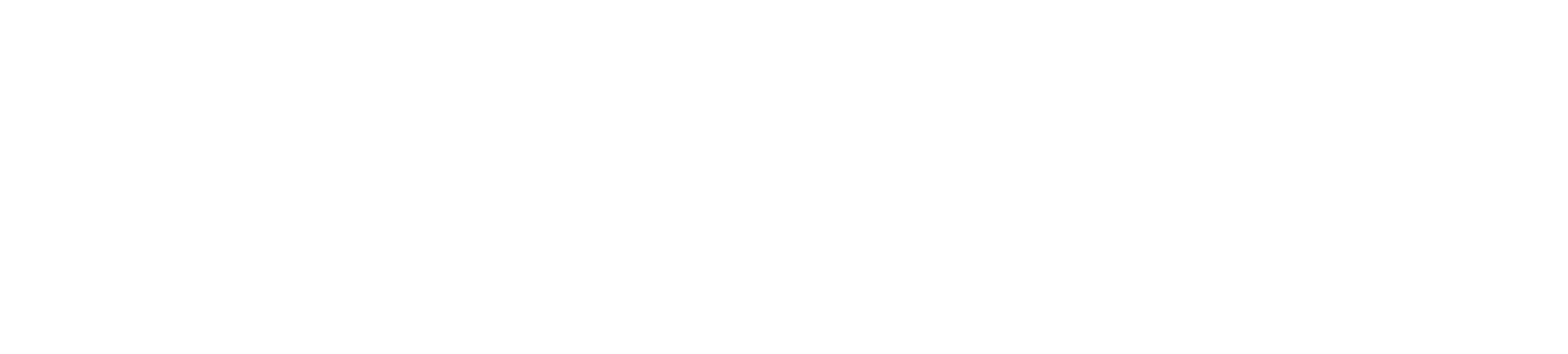