Do we still have a supply chain hangover after the pandemic?
In this edition of the Field Service News Think Tank Sessions, our focus was on digging deeper into a finding within a recent FSN Research study that revealed that 57% of field service companies surveyed stated that while they were able to access asset data, they felt they were not leveraging that data effectively.
As always in our Think Tank sessions, this initial starting point for the discussion led down many interesting avenues of debate, all of which are summarised in the executive briefing report currently available for a limited time on our forever-free FSN FREE subscription tier.
In this brief article, based on one section of that eighteen-page report, we focus on the impact the pandemic and subsequent lock-downs had on the global supply chain and ask if there are things we can do today to be prepared for such situations returning in the future.
In one respect, it is understandable that most companies are looking forward now after the pandemic. Indeed, from an emotive point of view, we must be able to move on in order to heal. Yet, there remain essential lessons from the challenges of the last two years that we must learn from, particularly around the supply chain that got disrupted on a global scale. Similarly, there remain lingering fears that we may see such disruption again, so we must be ready for it.
“The biggest thing for us in tackling supply chain issues was to rethink what we do regarding refurbishment.” explained Clinten van der Merwe, EMEA Service Director, Smiths Detection.
“Instead of just having a full spare parts replacement, we began looking at sub-component replacements on a spare part. This is certainly something important for us, and it helps with sustainability.
“I think this is probably the biggest denominator for us at the current moment because spare parts are getting harder to come by, you know, so it’s better to refurbish and repair whatever we can. This has also had a positive impact on our engineer efficiency as well as because our engineers when they sit in the airport can do some of the repairs on some IT equipment,” he added.
“I’m definitely hearing a lot about component repair at the moment and I think for some engineers, they’re quite enjoying it.” commented Mark Homer, Managing Partner, Field Service Associates.
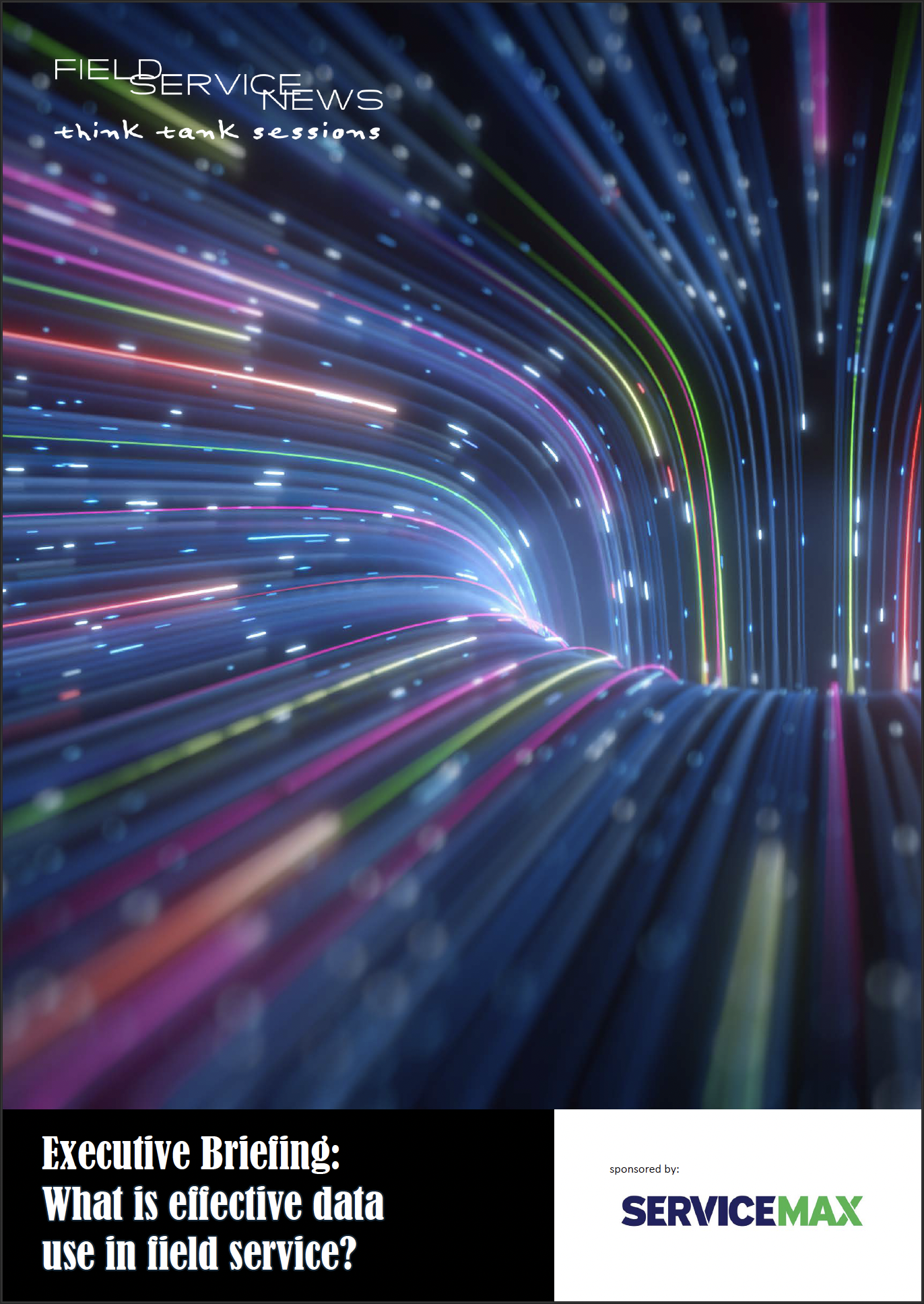
This content is available exclusively for FSN PRO members and will also be available on our FSN FREE subscription tier for a limited time. Please either log-in or subscribe on the button below for access.
Join FSN FREE today!
Subscribe to our forever-free subscription tier FSN FREE by completing the brief form below and get instant access to this resource plus a selection of premium resources every month.
[pmpro_signup submit_button=”Get access now!” level=”1″ redirect=”referrer” custom_fields=”true” short=”true”]
Data usage note: By accessing this content you consent to the contact details submitted when you registered as a subscriber to fieldservicenews.com to be shared with the listed sponsor of this premium content ServiceMax who may contact you for legitimate business reasons to discuss the content of this briefing report.
"What we've done concerning that is turn the data to the logistics team so that we give them the insight of what's likely to fail, and they can plan the capacity based on it." - Daniel Kingham, Elekta
“Definitely, component repair is probably the name of the game right now alongside obsolescence management so – recognising high value, high-risk parts and again this all comes back to data in terms of asset fleet analytics.”
Medical device manufacturer Elekta they are seeking to mitigate the problems of supply chain issues by utilising data to predict requirements more accurately.
As Daniel Kingham, Vice President and Head of Service Innovation and Design, Elekta explained.
“General supply chain constraints are causing problems without predictions; on the fact that even if we can predict they fail, we can’t necessarily supply the part.
“However, what we’ve done concerning that is turn the data to the logistics team so that we give them the insight of what’s likely to fail, and they can plan the capacity based on it.
“We’ve also changed the prioritisation of those parts, so where we can’t refurbish and can’t get parts to site, we’re constraining them on the basis that engineers like to stockpile and to order things when they know there’s a supply constraint. So we’re able to give a lot more guided information to say actually, we don’t believe you need this yet. So far, it is an approach that is working.”
While the hope is that the events of the last two years are a once-in-a-generation situation, it is always best to be prepared. Yet as we saw in the discussion, there are benefits in efficiencies, so it is a win-win situation.
If you wish to read more from the group on how the challenges, benefits and barriers to effective use of asset data, then download the full executive briefing now (available for a limited period on our forever free subscription tier FSN FREE)
Do you want to know more?
If you are already a subscriber you can access the report instantly on the ‘read now’ button below. If the button is showing ‘Join FSN FREE’ please log-in and refresh the page.
If you are yet to subscribe simply click the button below and complete the brief registration form to subscribe and you will get instant access to this report plus a selection of premium resources each month completely free.
Join FSN FREE today!
Subscribe to our forever-free subscription tier FSN FREE by completing the brief form below and get instant access to this resource plus a selection of premium resources every month.
[pmpro_signup submit_button=”Get access now!” level=”1″ redirect=”referrer” custom_fields=”true” short=”true”]
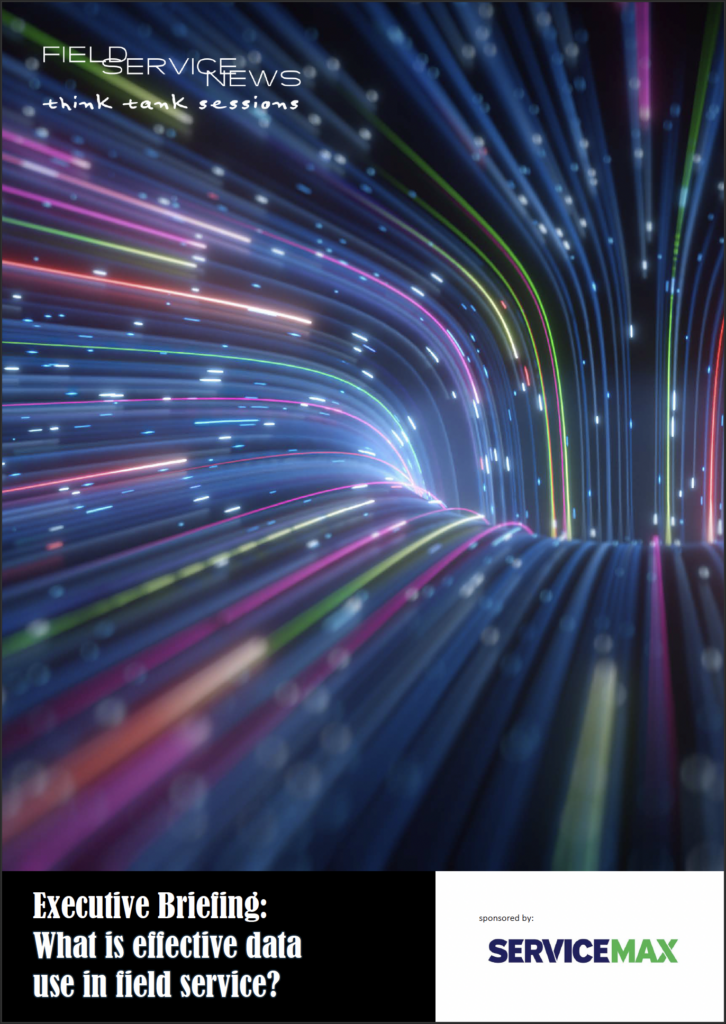
Data usage note: By accessing this content you consent to the contact details submitted when you registered as a subscriber to fieldservicenews.com to be shared with the listed sponsor of this premium content ServiceMax who may contact you for legitimate business reasons to discuss the content of this briefing report.
Many thanks to our Think Tank members present during this session.
- Sumair Dutta, Senior Director, Product Marketing – Customer and Market Insight, ServiceMax
- Mark Homer, Managing Partner, Field Service Associates
- Rajat Kakar, Managing Director, QuickWork EMEA
- Chris Hird, Editor, Field Service News
- Dave Hart, Managing Partner, Field Service Associates
- Daniel Kingham, Vice President and Head of Service Innovation and Design, Elekta
- Mark Homer, Managing Partner, Field Service Associates
- Mark Wilding, VP Global Customer Transformation, ServiceMax
- Terence Horsman, COO, Orca Service Technologies/MCFT
- Clinten van der Merwe, EMEA Service Director, Smiths Detection
All members of the Field Service Think Tanks are speaking from their own personal opinions which are not necessarily reflective of the organisations they work for.
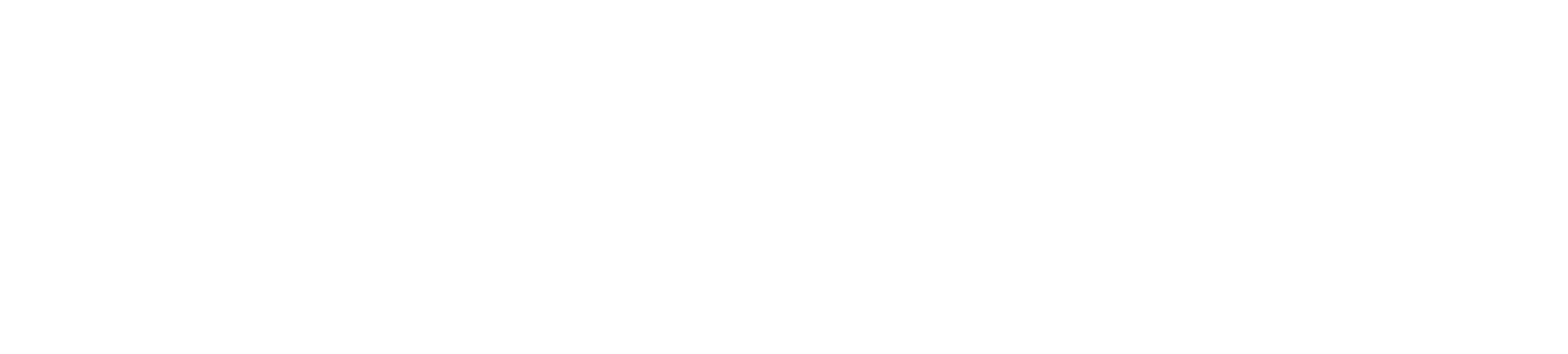