Four Service Scenarios: #1 The Equipment-Centric Scenario
In the first of four deep-dive features where we explore the four service scenarios Gartner defined as being dominant in field service across the next five years we look at equipment-centric service scenarios…
Defined by Gartner as a scenario where there is a ‘certified expert focus on complex equipment, telemetry and regulations,’ the equipment-centric scenario for field service delivery sits comfortably within the modern approach of field service management and is growing in popularity.
Such growth is, of course, aligned with the increase of asset data that is now available to be transmitted remotely via IoT. Essentially, we can now know far more about our assets and their performance in real-time than we have ever been able to do in the past.
Equally, with the vast swathes of asset data available for analysis, and the technology readily available to help drive meaningful insight out of that data, potentially across an entire install base, we can continuously refine best practices for genuine optimisation of the asset’s performance.
However, having asset data and the tools for broad-reaching analysis of that data is not necessarily enough on its own. There is a need for context when looking for insight within data, and that context is likely to be found in those with deep-level subject matter expertise in both the assets themselves and how they are being utilised.
Indeed, many of the most successful organisations to have leaned into such an approach have found a balance between data science and operational expertise, with examples of collaboration between data teams and an engineering team, while still being relatively uncommon, starting to be discussed more frequently.
Such approaches to better understanding how to optimise equipment performance through data-driven, proactive service and maintenance are appealing for those customers whose asset is not just complex but also plays a significant role in revenue generation.
In the oil and gas sector, for example, the uplift in revenue from, say, a turbine operating at an optimum can be significant. In high-stakes sectors, even a slight boost in productivity can have an incredible effect on top-line revenue and bottom-line profits.
The flip side of this is that any unplanned downtime on such an asset can significantly affect customer revenue. Therefore, within an equipment-centric scenario, the expectation from the customer is likely to be set around a proactive, preventative maintenance policy.
In such an environment, no matter how tight an SLA, if the service is delivered on a break-fix approach, then by the time the issue is resolved, revenue will already be lost – and when revenue is on the line, then serious questions get raised by the customer about the suitability of the service provider to support their business moving forward.
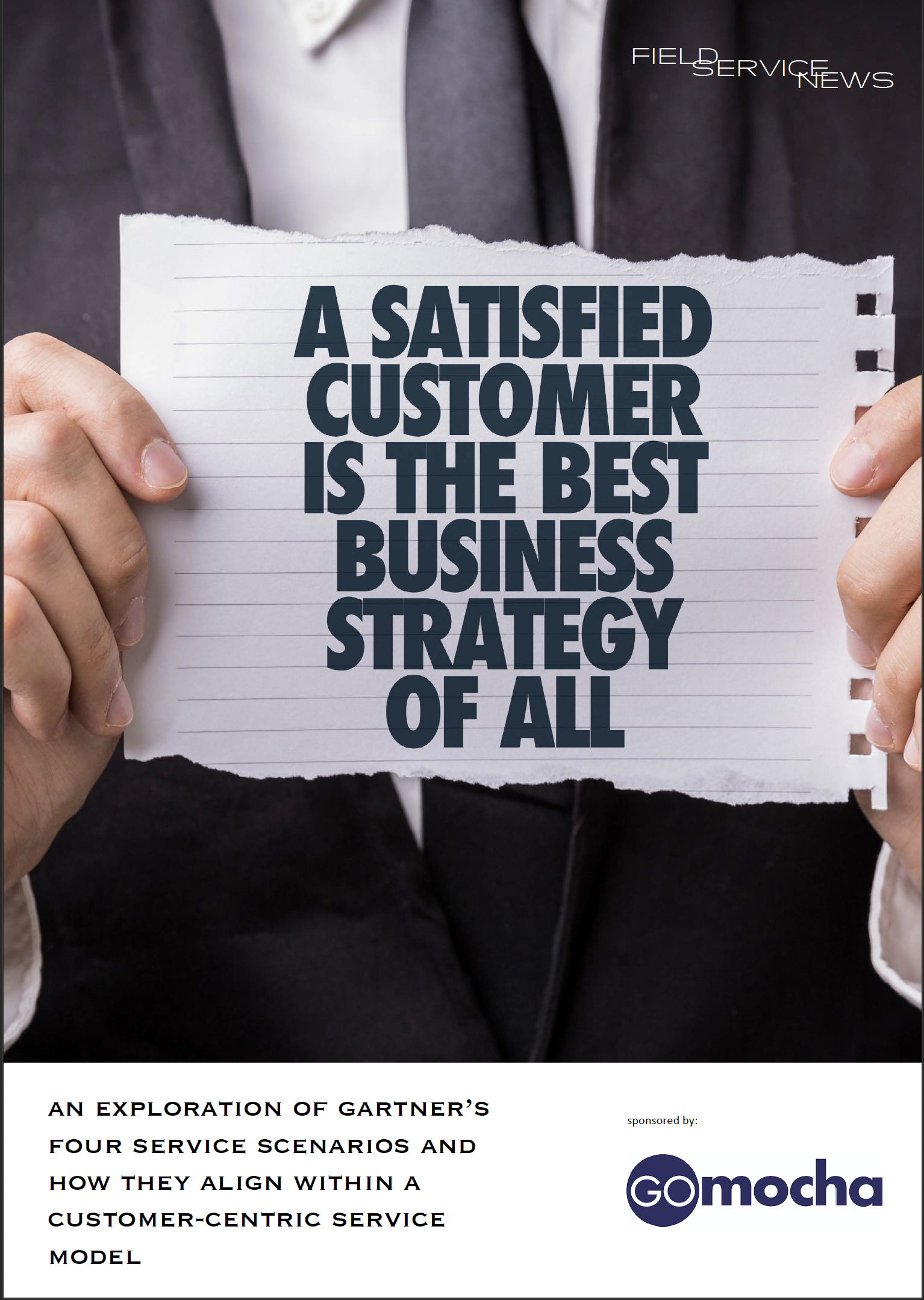
Data usage note: By accessing this content you consent to the contact details submitted when you registered as a subscriber to fieldservicenews.com to be shared with the listed sponsor of this premium content Gomocha who may contact you for legitimate business reasons to discuss the content of this briefing report.
This content is available for FSN PRO members and also for a limited period for FSN FREE members. Please make sure you are logged in to access this content.
Not yet subscribed? Instantly unlock this content and more on our forever-free subscription tier FSN FREE
"There is a need for context when looking for insight within data, and that context is likely to be found in those with deep-level subject matter expertise..."
Of course, one of the widely touted benefits of being able to extrapolate intelligence from connected assets is the ability to much more accurately predict mean-time-to-failure based on the data received from the asset.
For organisations with this capability, the preventative maintenance model is much more viable. In the past, preventive maintenance models often resulted in many unnecessary service calls, where a highly skilled and valuable service engineer would travel onsite to perform a health check on the asset – which could be an expensive and largely unnecessary exercise if there was nothing wrong.
In a data-driven era, such service calls are no longer required. Instead, the asset can be monitored remotely, and an engineer dispatched only when needed.
However, when building our service contracts around being equipment-centric, it is highly likely that the customer expects the engineers who attend to their assets are certified subject matter experts.
Therefore, while it is feasible for such expertise to be delivered remotely, whether that is to an internal field-based colleague, a certified third-party contractor or the customer’s in-house technicians, the reality is that an equipment-centric scenario would still potentially rely on the OEM or service provider delivering onsite service, maintenance, and optimisation via an engineer with deep-levels of subject matter expertise.
Therefore, the emerging remote-first approach to service wouldn’t likely be a fit within an equipment-centric approach to field service management – something that would need to be considered in adopting an approach as remote-first is being championed by many as not only resolving issues faster but also doing so at a reduced cost to the service provider and as such has gained much traction, particularly since the pandemic.
One final aspect for consideration is parts management.
Suppose a service organisation is basing their service contracts around highly specialised engineer knowledge that allows for a proactive approach to maintenance and optimisation. In that case, the ability to ensure any required
“we should be sending our engineers to the customer site with a clear picture of how the asset is performing, including which parts are nearing their life-cycle expiration, which consumables may be required, and of course, any potential faults...”
In a data-driven era, such service calls are no longer required. Instead, the asset can be monitored remotely, and an engineer dispatched only when needed.
However, when building our service contracts around being equipment-centric, it is highly likely that the customer expects the engineers who attend to their assets are certified subject matter experts.
Therefore, while it is feasible for such expertise to be delivered remotely, whether that is to an internal field-based colleague, a certified third-party contractor or the customer’s in-house technicians, the reality is that an equipment-centric scenario would still potentially rely on the OEM or service provider delivering onsite service, maintenance, and optimisation via an engineer with deep-levels of subject matter expertise.
Therefore, the emerging remote-first approach to service wouldn’t likely be a fit within an equipment-centric approach to field service management – something that would need to be considered in adopting an approach as remote-first is being championed by many as not only resolving issues faster but also doing so at a reduced cost to the service provider and as such has gained much traction, particularly since the pandemic.
One final aspect for consideration is parts management.
Suppose a service organisation is basing their service contracts around highly specialised engineer knowledge that allows for a proactive approach to maintenance and optimisation. In that case, the ability to ensure any required replacement parts are always available to the engineer ahead of the visit becomes critical. In a proactive service model, an engineer having to return at a later point because of a lack of parts availability negates much of the benefit.
Of course, one solution that has been utilised in the past is to ensure there is adequate ‘van-stock’ so the field service engineer generally has the parts on hand. This, of course, comes with challenges that are certain to be magnified in the current economic period as this ties up significant cash on the P&L and unless a dedicated Field Service Management system that is capable of tracking van-stock effectively is in place, such an approach can result in missing inventory which can ultimately create a black hole cash on the P&L.
Again, this is where effective use of data can significantly improve our processes. In this regard, we can leverage data two-fold. Firstly, in parts data itself. Knowing what is where is essential, and yet while relatively simple to achieve, spare parts information remains a woefully underdeveloped aspect of field service operations for many field servicre organisations.
However, we can also improve our spare-parts usage when we look at the data-driven pro-active approach to service that we see in the equipment-centric approach.
Through the use of asset data, we should be sending our engineers to the customer site with a clear picture of how the asset is performing, including which parts are nearing their life-cycle expiration, which consumables may be required, and of course, any potential faults that the data shows signs of emerging that can be resolved ahead of failure.
In summary, if an organisation were to take an equipment-centric approach to field service, they should consider the following:
- Are they able to receive data from their assets in the field?
- Do they have the capability to monitor this data in real-time and draw meaningful, actionable insight from them?
- Does the organisation have the personnel, structure and resources to move beyond simply providing maintenance ahead of failure and to begin optimising asset performance? How big a value proposition would this be for their customers?
- Do their field engineering teams have industry-leading subject matter knowledge? Is this a widely known fact in their industry?
- Are their FSM systems suitable for proactive service models – in terms of scheduling engineers and parts?
Do you want to know more?
If you are already a subscriber you can access the report instantly on the ‘read now’ button below. If the button is showing ‘Join FSN FREE’ please log-in and refresh the page.
If you are yet to subscribe simply click the button below and complete the brief registration form to subscribe and you will get instant access to this report plus a selection of premium resources each month completely free.
This content is available for FSN PRO members and also for a limited period for FSN FREE members. Please make sure you are logged in to access this content.
Not yet subscribed? Instantly unlock this content and more on our forever-free subscription tier FSN FREE
Join FSN FREE today!
Subscribe to our forever-free subscription tier FSN FREE by completing the brief form below and get instant access to this resource plus a selection of premium resources every month.
[pmpro_signup submit_button="Get access now!" level="1" redirect="referrer" custom_fields="true" short="true"]
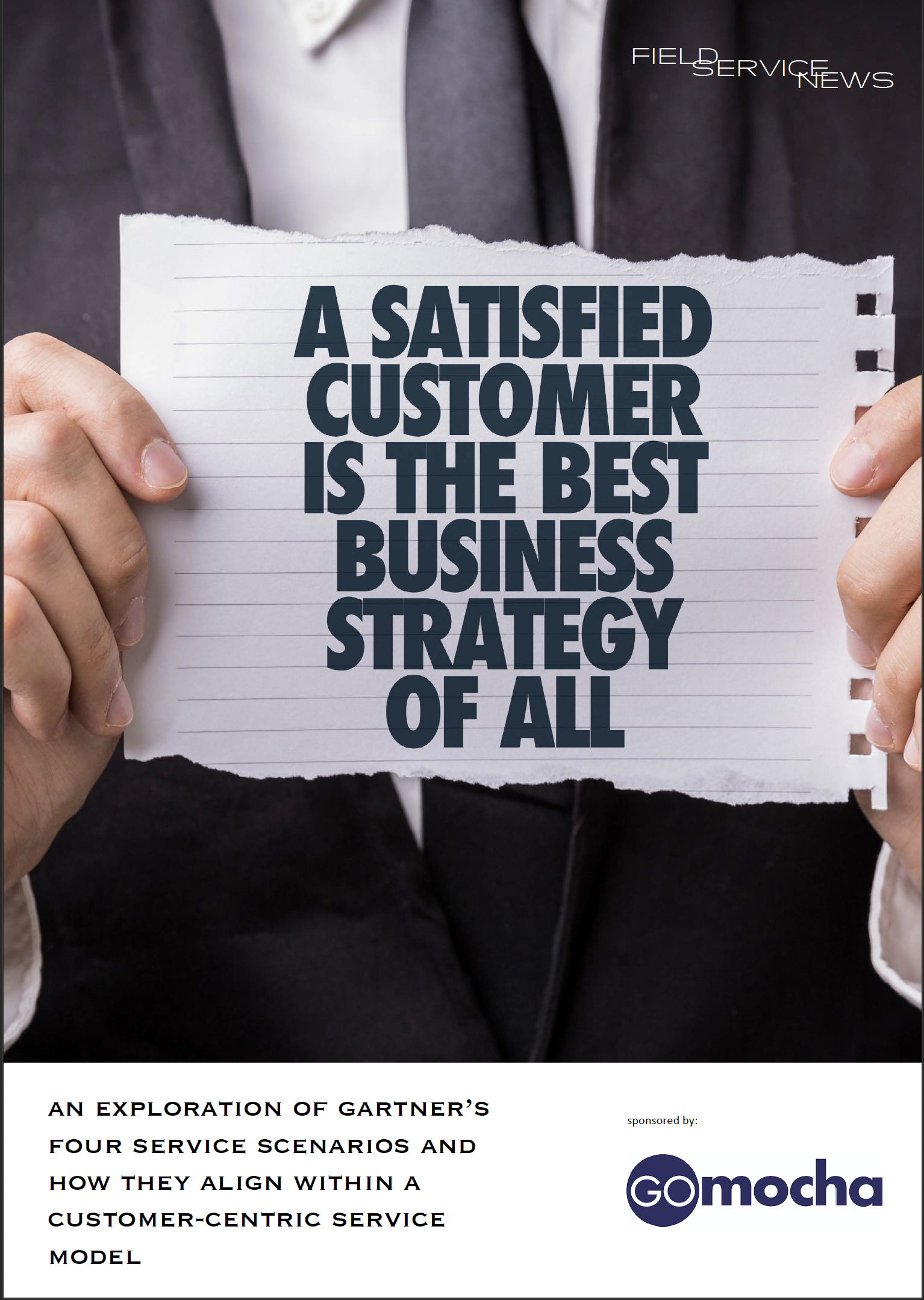
Data usage note: By accessing this content you consent to the contact details submitted when you registered as a subscriber to fieldservicenews.com to be shared with the listed sponsor of this premium content Gomocha who may contact you for legitimate business reasons to discuss the content of this briefing report.
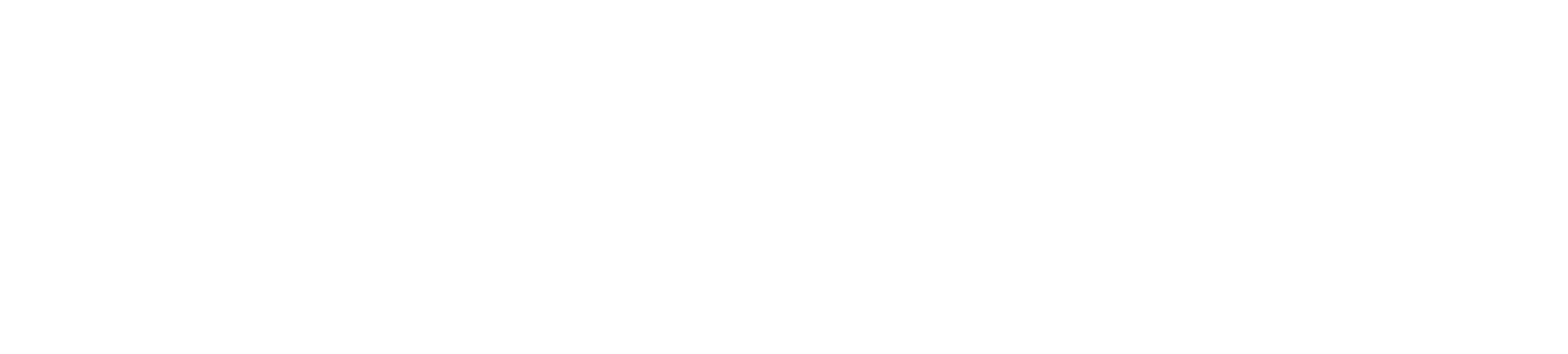