Keeping Cancer Treatment Systems Treating
Daniel Kingham, Predictive Maintenance & Intelligence Director Elekta shares his insight in to the crucial role Elekta IntelliMax plays in keeping the important cancer treatment operational even during the global Covid-19 pandemic.
Individuals waiting for – or even right in the middle of – a radiotherapy session to treat their cancer likely have other things on their mind than the possibility that their therapy could be delayed or stopped due to equipment malfunction.
But with any sophisticated machine that relies on software, many moving parts, a vacuum system, water cooling, and high voltage, the chance that the linear accelerator and associated systems will suffer a functional issue is always lurking.
The global COVID-19 pandemic has further accentuated the need for predictive remote support to maximize clinical uptime, keeping vulnerable patients, hospital staff and Elekta personnel safe.
Fortunately for our customers, Elekta IntelliMax® is standing guard, always connected, always ready to pinpoint issues that could disrupt the patient’s timely treatment.
This advance warning enables Elekta service personnel to follow prescriptive actions to replace parts before they fail. It also provides secure remote access for proactive resolution using advanced diagnostics, often before the customer has raised the issue. This maximizes clinical availability, minimizes costs and reduces the chance of disruption for patients. In 2019, more than 3,000 IntelliMax-generated cases were raised to avoid clinical interruptions and downtime.
It was the ability of IntelliMax to predict issues and enable proactive resolution – resulting in thousands of hours of avoided clinical downtime – that contributed significantly to Elekta winning the 2019 Technology Services Industry Association (TSIA) STAR Award for Best Practice in Field Service.
Three Waves of Change
Getting to this point however has been a long process with many lessons learned along the way and numerous growing pains. Technology, suppliers, our products, and our customer needs are continuously evolving, creating new opportunities for connectivity and bringing new challenges along the way.
In the last 14 years, among the biggest changes from a customer perspective has been the evolution of data security and connectivity. We’ve seen three distinct waves of security challenges.
Back in 2004, the first wave was demonstrating to customers the value of allowing us to connect to the devices. We had to demonstrate utility. Expanding connectivity within our installed base was slow.
The second wave occurred after 2006 with broader acceptance of connected devices. We saw a trend within new customers asking us to connect to treatment machines. Over this period, we saw exponential growth in connected devices, which is why today over 80% of devices are connected in more than 80 countries.
Recently we have entered the third wave, which is the maturation and growth of IT departments and concern for cybersecurity and data breaches. Elekta maintains simple enforced rules as part of our “privacy and security by design” mandate. For example, no patient data are ever allowed to be uploaded. We continue to evolve how we comply and expand on these capabilities.
With the advent of General Data Protection Regulation (GDPR) in Europe and the strengthening of HIPAA rules in the USA, we have been able to respond quickly and demonstrate why we believe we have a compliant means of remote monitoring.
Big Data and Artificial Intelligence
From an organizational perspective, a key learning has been in deciding whether to outsource or insource data analytics. Initially, we thought we could partner with external experts to use our data and build predictive maintenance models and alarms. What we learned – due to the unique and complex nature of the devices – was that the most cost-effective way to scale was to insource and invest in an internal team that understood the products and how they operate.
This has created a continuous feedback model in which every service engineer can share positive and negative experiences to help us continue the improvements to ensure we meet our customers’ need to plan maintenance in advance.
This internal expertise helped accelerate our use of artificial intelligence (AI). Over the last three years our data science teams have built a variety of machine learning algorithms and filed multiple patent applications.
Our AI algorithms raise 75 percent of predictive cases, and thanks to our continuously improving AI model, new use cases are being piloted and refined all the time – a first in our industry. Notably, Elekta is the only radiotherapy company to employ AI-driven predictive technology for service with multiple patents pending.
Service in the COVID-19 era
Most recently, COVID-19 has created brand new challenges and opportunities for improvement. As a global company, Elekta immediately identified a need to provide more remote support and minimize exposure of service personnel – initially in hospitals in China, and now across the globe, to protect our field service engineers (FSE) and vulnerable patients.
Many facilities around the world have postponed planned maintenance activities. The need for more personal protective equipment (PPE) and more sterilization to reduce risk of transmission has extended treatment set up times, reducing access availability for maintenance.
Our predictive capabilities have assisted in predicting parts demand and in the logistics challenges of freight constraints and parts availability in different countries. Also, to minimize time on site, when there is a part failure due to deferred maintenance, the FSE can arrive with the exact part needed to resolve the issue, instead of spending time on diagnostics or awaiting shipment of multiple possible parts.
Finally, we have seen an increase in proactive remote fixes globally, which means we are helping reduce clinical downtime and helping reduce transmission risk. Customers are also increasingly expecting remote support, a trend we hope will continue long after COVID-19 subsides.
A Bright Future
It has been incredibly rewarding to see the hard work and vision become reality over the past few years with recognition from TSIA. We have learned many lessons along the way, and as a result we have been able to apply the same principles and frameworks to bring predictive maintenance to our pure software products, focusing on how to relieve the customer pain points each step of the way.
The team making this possible has grown and evolved from initial early use cases with a handful of connected systems, to a mission-critical operation that delivers demonstrable benefits to our customers and their patients. It makes me incredibly proud to lead a team that drives change in our organization, and to be part of a much wider team that make this possible – from the developers and product management in our engineering organization, to the FSEs and service center staff who work tirelessly to keep treatment machines operating.
Everyone at Elekta plays a part.
#FSN20 is an annual celebration of excellence, innovation and leadership shaping the global field service sector. This content is proudly sponsored by Salesforce.
#FSN20 is an annual celebration of excellence, innovation and leadership shaping the global field service sector. This content is proudly sponsored by Salesforce.
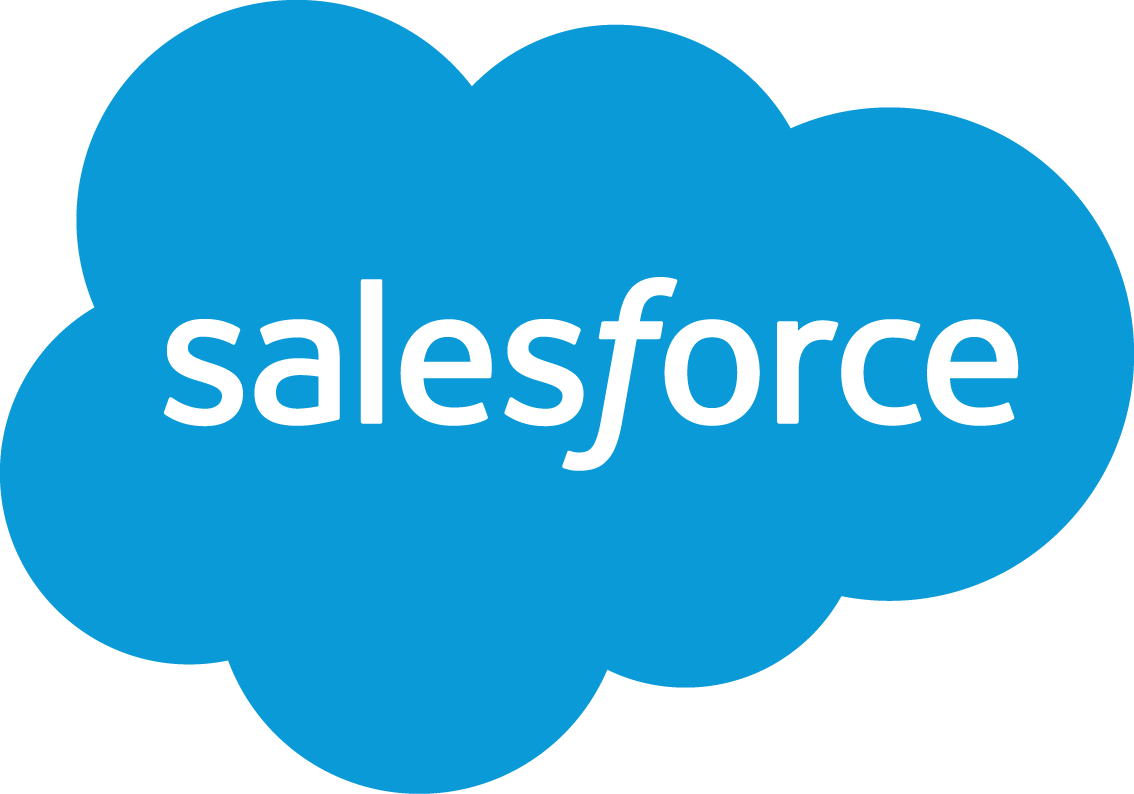
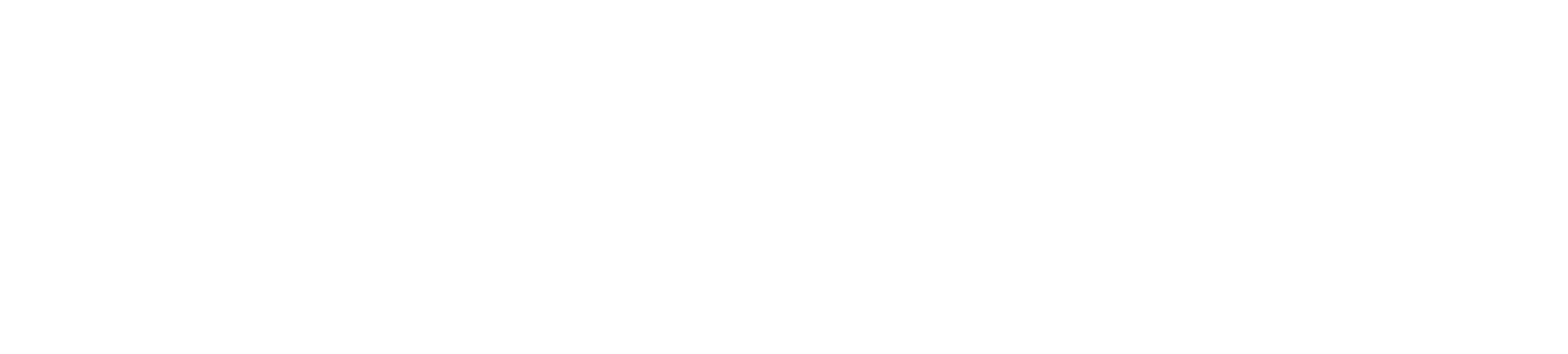