The Big Discussion: Dynamic Scheduling - Part 2.
In the Big Discussion we bring together a panel of industry experts and focus on one key topic within the field service sector. In the third of a four part series on dynamic scheduling our panellists, FieldAware’s Marc Tatarsky and Fast Lean Smart’s Chris Welsh identify the biggest mistakes companies make when implementing a scheduling system.
Question: Should optimised scheduling still be considered as a best-of-breed solution or should it now be an expectation of wider FSM platforms?
Marc Tatarsky, SVP Marketing, FieldAware
The most significant expense for a service organisation is the cost of its field resources. In a hyper-competitive market where service delivery is a crucial differentiator, service organisations must excel at customer service delivery whilst sustaining high levels of operational productivity.
Given these increased pressures, an optimised scheduler is a core feature of any world-class FSM platform. Ensuring work schedules are compliant, deliver the intended service to the end customer, and are operationally efficient is essential. Traditionally, providing this depth of capability was cost-prohibitive for an FSM platform. Implementation projects were either too lengthy or too complex to configure an optimizer efficiently.
Modern, micro optimisation capabilities enable service delivery companies to quickly and cost-effectively implement optimised scheduling at a team level. Moreover, for those workflows needing a manual or semi-automated scheduling, advanced FSM tools also provide options such as Planning Mode. This capability allows schedules to be built and adjusted in a safe environment either manually or through interactive optimisation cycles. When the Planner or Dispatcher is satisfied with the scheduling outcomes, they can publish and dispatch the approved schedule to the field technician’s mobiles following the team’s dispatch policy.
Chris Welsh, Director, FLS – FAST LEAN SMART
Making do with scheduling included in an FSM platform might seem logical, however the benefit can be so great that best-of-breed is the way to go. Not only does schedule optimisation minimise cost, it also helps ensure you can deliver on the increasing service expectations of your customers.
In 2019, I believe it reasonable to set the minimum bar at the following capabilities to describe field service scheduling as ‘optimised’:
- Dynamic schedule optimisation to incorporate all engineers and jobs over a substantial radius, not just assigning work to an engineer because it’s their patch or have a space to fill in the diary;
- Route calculation with actual average driving speeds for each road segment according to the time of day.
FLS are one of the few companies with this expertise, honing our solutions for over 25 years to provide the fastest, leanest and smartest configurable algorithms that can be integrated easily into any established FSM solution or new project.
Our customers are using most of the leading FSM/CRM/ERP technologies and FLS are happy to prove the benefit free of charge, starting with a scheduling test to compare how FLS VISITOUR would have scheduled your work – expect to be amazed at the unlocked potential!
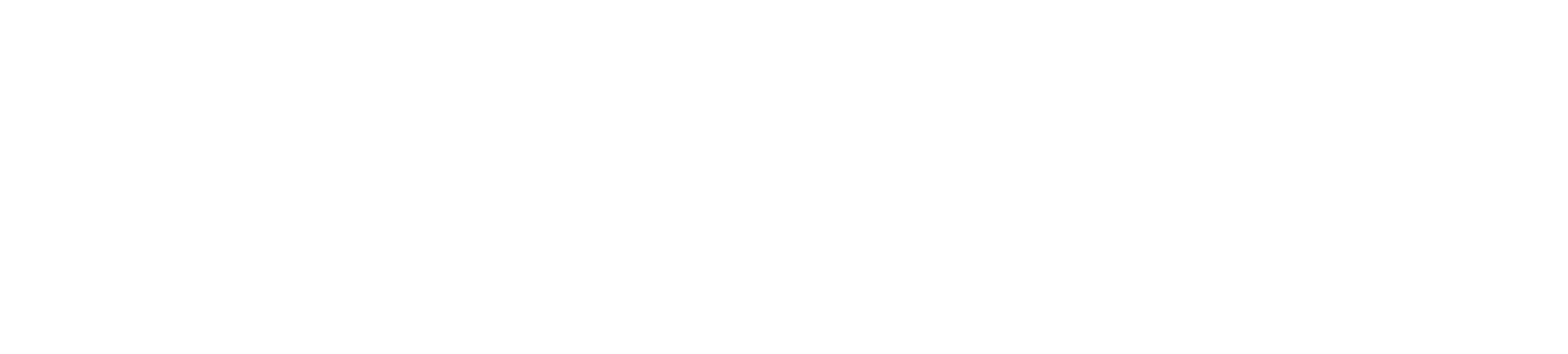