ThinkTank Reflections: The need for better data protocols is becoming more and more pressing...
ThinkTank Reflections: The need for better data protocols is becoming more and more pressing...
Establishing data integrity for practical application in modern field service systems is an important area of focus for field service organisations moving forward.
Still, progress in this area will undoubtedly be limited in scope when multiple data protocols exist within industry verticals. For third-party service providers, in particular, this challenge threatens their ability to meet increasing customer expectations.
This was a significant area of discussion in a recent iteration of the Field Service News ThinkTank sessions, where we explored how much the field service sector has changed over the last two years.
“We use customer IoT devices, and everyone has different standards,” explained Gyner Ozgul, President & COO, Smart Care Equipment Services.
“Unfortunately, our industry hasn’t had a standard unification yet. There is some in HVAC, but in our industry, every manufacturer, sometimes the customers themselves and then third-party intermediaries, all have different asset management standards. Because of that, there’s a lot of complexity. Do you use the serial number of the piece of equipment? Do you use an asset tech number for the customer view?” Ozgul continued.
“All of these variables, all add a lot of complexity to the both the asset management itself and then into the insights that asset data can carry forward throughout the organisation,” he added.
“This is a major challenge anybody who is not the original OEM faces – they struggle with coming together with a standard IoT adoption policy,” agreed Tom DeVroy, Senior Advisory Solution Consultant, ServiceNow.
“Everybody wants their own sensors, their own methods for monitoring their equipment and it makes it virtually impossible for an organisation like that to effectively utilise a lot of those readings they can get from those sensors and disseminate it so they can make sense of it without spending tons of money,” he added.
“We service our own equipment, as well as non-Konica Minolta equipment,” commented Izzy Sanchez, Director of Service & Systems Support Konica Minolta.
“We have something called the RMS platform, which is a device relationship management platform. The level of effort it took us to develop that platform was insane because our competitors would not give us that information,” he explained.
“So we had to find a way to normalise the data. When a job comes in, what component is it related to, how much can we use the insight we have in our team, and also take an educated guess where needed. However, now the technology on the back end, the AI, is catching up, and it can start joining many of the dots, looking at curves and doing other clever things.
“It’s important that if you don’t get the buy from OEM’s or industry at large, then at some point, you have to start considering a strategy to normalise that IoT signal for your particular industry. I think that would that will go a long way, to over coming the challenges but it is very painful,” Sanchez advised.
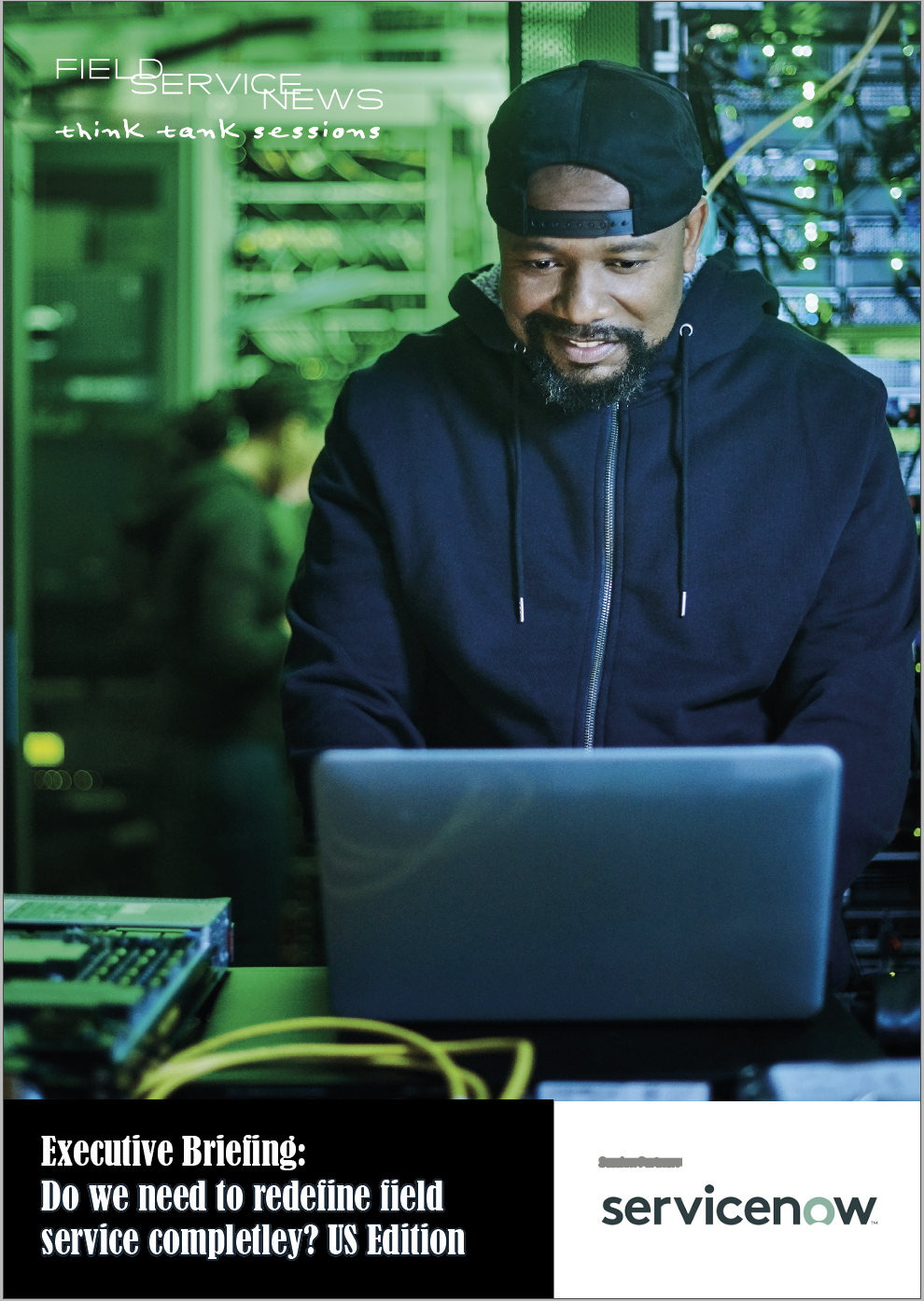
Want to know more?
This content is available exclusively for FSN PRO/PRO+ members. If you already have a valid membership but cannot see the watch now button below, please ensure you are logged in to access this content.
Not yet subscribed? Instantly unlock this content and over 600+ hours of industry-leading education with FSN PRO now!
SIGN UP TODAY! Use the code TRIAL9 to claim an incredible introductory offer for your first month for just £9 (regular price £45)
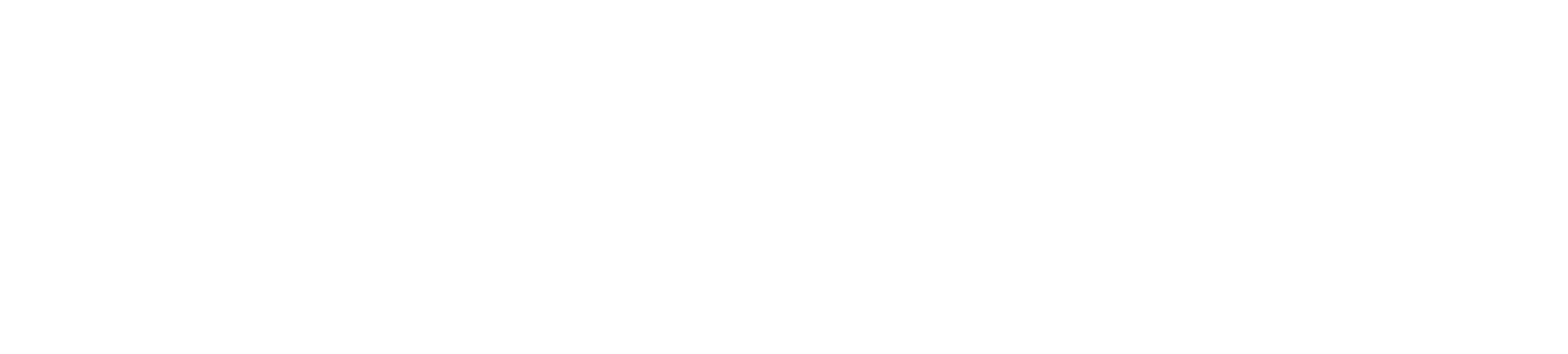