Supply Chains Grinding to a Halt as Borders Came Crashing Down
With operations being so suddenly impacted the financial implications of the pandemic on our sector were profound and wide-reaching. As we assess the damage done to our sector, it was apparent that the issues we faced were echoed across almost every sector and the challenges faced in terms of economic impact would be felt for a long time…
Much has been said about the benefits of a truly global economy, and many strides have been made towards globalisation. Since the dawn of the internet, the world has become smaller, and the global village has expanded as have the operations of most companies into far-flung areas of the world far from home.
Supply chains have been established as multi-national entities for as long as we can remember, so what happens when suddenly borders are closed, and that supply chain slows right down?
As Tony Chapman, General Manager, Customer Services, Siemens commented. “A significant pillar of our operation is the management and distribution of spare parts. We’ve touched on the impact of the supply chain and this was a real area we had to focus on quickly as it had the potential to have a dramatic affect on our business.
“Our spare parts provision is well optimised, but we rely heavily on centralised storage and then moving things very quickly to the site when required. So we have all the processes in place to get things from our storage facilities to the UK, typically overnight, for example.
“But again, the real challenge was the sudden increased delays in that process. Fortunately, we have a really strong team in that area, and we were able to get that resolved fairly quickly.”
“Ultimately, if the supply chain end to end chain is not working this impacted organisations and the results were felt by consumers…”
– Rajat Kakar, IBM
In fact, perhaps one of the biggest impacts of the global lockdowns was the domino effect on the supply chain as various links in a chain that until 2020 had seemed robust and reliable suddenly became exposed to vulnerabilities.
As Rajat Kakar, IBM explained, “The impact of the Covid-19 on supply and demand across different sectors was complex compared to the first glance. As an example, looking at the ‘toilet paper’ industry – what happened during Covid-19 if you were a producer of toilet paper for homes – you saw everything vanish from the stores due to skyrocketing demand. Consumers just ran out and bought toilet paper.
“Now, imagine the situation at the toilet paper producers for hotels, for restaurants, for office buildings – there were big rolls of toilet paper just sitting there, not moving at all. These producers for consumer and corporate might have been the same companies, or, they were undoubtedly using similar suppliers at some point within the supply chain. Ultimately, if the supply chain end to end chain is not working this impacted organisations and the results were felt by consumers.”
Fortunately, governments and corporations alike were able to react quickly to prevent the supply chains staying closed for a prolonged period. However, in the wake of the challenges we saw emerge, many companies, including some of those within the Think Tank, are now undergoing a considerable rethink of their logistics solutions to ensure that should the worst happen and we see similar lockdowns in a second wave they are not once again caught out.
The pandemic has brought about much change and much innovation, when it comes to the service supply chain, an area often overlooked within field service conversations, it is perhaps the most important aspect of whatever the new norm is to be. Whether it be embracing 3D printing, investing in parts and inventory management tools or ensuring a more localised network of storage facilities, these are critical discussions that must take place for the industry today.
All members of the Field Service Think Tanks are speaking from their own personal opinions which are not necessarily reflective of the organisations they work for.
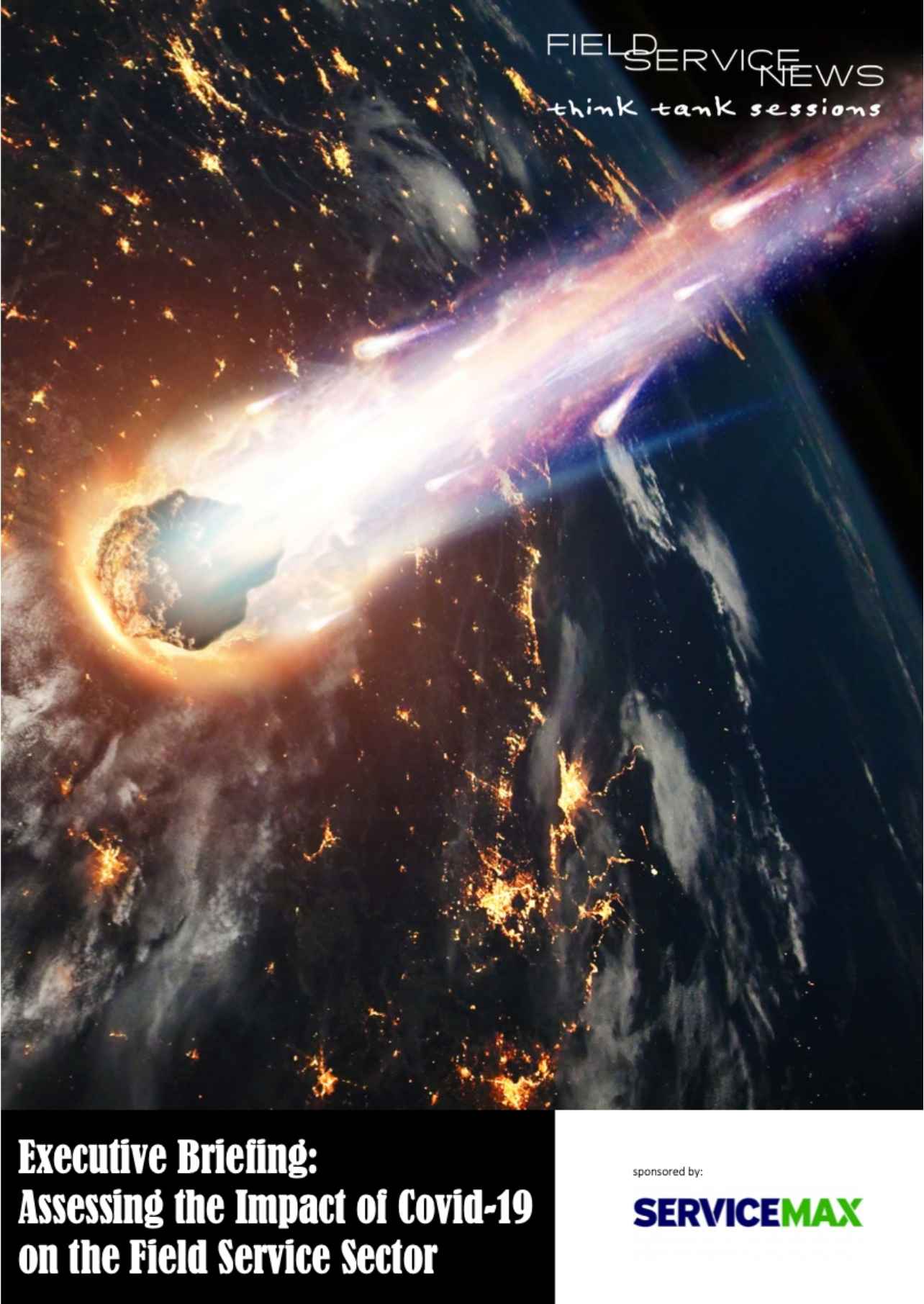
Data usage note: By accessing this content you consent to the contact details submitted when you registered as a subscriber to fieldservicenews.com to be shared with the listed sponsor of this premium content Service Max who may contact you for legitimate business reasons to discuss the content of this briefing report.
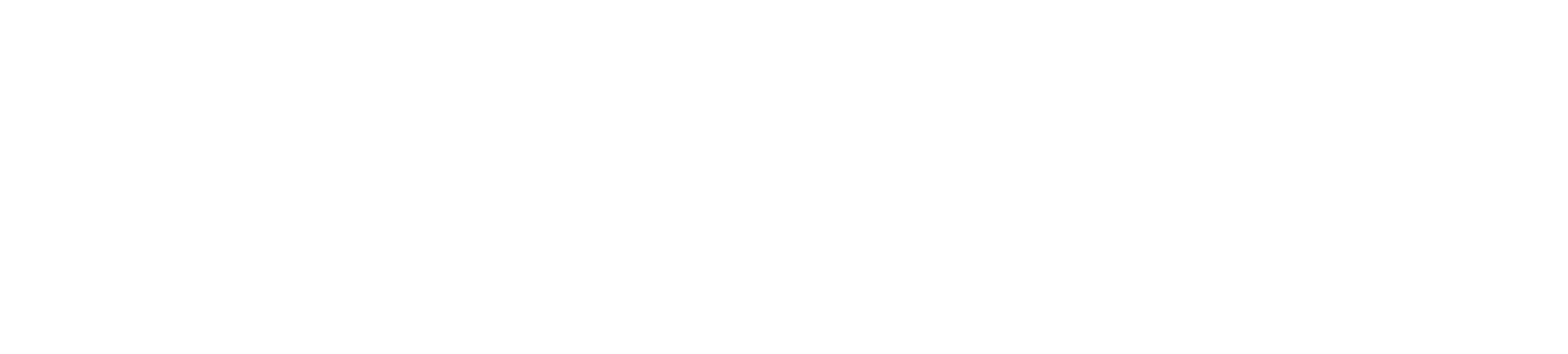